- An independent free-standing unit with elevating roller deck platform to raise and lower ULD containers between multiple system levels
- Uses electrical hoisting mechanism with 20mm wire ropes.
- Winch gear is floor mounted for ease of maintenance (can be mounted overhead if space is a constraint)
- Hoist motor/gearbox arrangement has an electromechanical brake system to support the load when not at base level.
- Full range of safety mechanisms
- Optional operator walkways and control station on the deck for maintenance
- Absolute horizontal and vertical positioning to +/- 1mm
- Fully automatic operation
WE GO THE DISTANCE
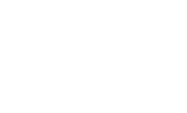
Elevator for air cargo ULD / Pallets
Features:
ULD / Pallet Elevator
Description:
This is an all-electric operation, roller deck lifting platform designed and constructed to receive, hold and transfer ULDs and pallets of <14,000 kgs between system levels. The Elevator can interface with manual or powered equipment at all levels within the Client’s system.
Technical Data:
Load Capacity |
‹14,000kgs |
Elevation Speed |
30 meters per minute |
Roller Deck Transfer Speed |
18 meters per minute |
Safety Sensors |
Overhanging containers from Elevator deck Over height control Pallet sensors Elevator door closed check |
Safety Systems |
Platform Grab, over-speed governor Emergency Stop buttons Interface with elevator shaft doors / gates Safety fencing Audible and visual alarms |
Emergency Fall Back |
Hoist drive brake releases Platform lowering Deck drive brake release |
Specifications:
The vertical height measuring is achieved using linear encoders. The BDP designed control system therefore has absolute positional information with positioning accuracy of +/- 1mm. Limit switches also ensure no overrun in the unlikely event of positioning system failure
The Elevator comprises of a heavy-duty shop-welded base frame and free-standing superstructure fixed to the warehouse floor on its own mounting plates.
The elevating roller deck comprises of a heavy-duty steel shop welded frame suspended from lifting wire ropes used to raise and lower the platform to various interfacing levels.
Non-slip operator walkways are installed between rollers to enable operators and maintenance staff to safely enter the lift platform.
Full width guides are installed on both sides of the roller deck with operator non-slip walkways, sufficient to allow operator to pass with a full-sized unit on the deck.
To control safe movements of the freight, photoelectric pallet sensors are installed at each end of the deck platform.
Hard wired travel limit systems are provided at upper and lower positions to prevent lifting platform overrun.
Emergency stop buttons are located at principal maintenance points and at each of the operators control consoles. Automatic safety grab systems are integrated into the lifting system to prevent fall of roller deck in the event of hoist system failure.
Maintenance props are integrated in to the lifting platform to hold it horizontal, under full load conditions.
A CCTV system can be installed, with monitors at the operator control stations, to allow operator to view
inside the lift shaft.
A “key” controlled override system is made available to override normal safety systems. These must only be used in extreme conditions and by a specially trained supervisor.
ULD / Pallet Elevator
Print Document
Equipment Links
- Non-Powered Roller Deck (GRC)
- Shuttle vehicle
- Turntable
- Truck Dock
- Right Angle Transfer Deck
- Lowering Workstation
- Surface Mounted Drop Bed (No pit required)
- Split Lowering Workstation
- Elevating Transfer Vehicle
- ULD Elevator
- 10ft Slave Pallet
- LD3 Slave Pallet
- Manual Ball Mat
- Manual Caster Deck
- PLC Control Systems